MAG develops novel process to produce giant gear
Source From: MAG
Posted Date: 2011-06-01
Horizontal boring mill and special tooling used to cut gear teeth
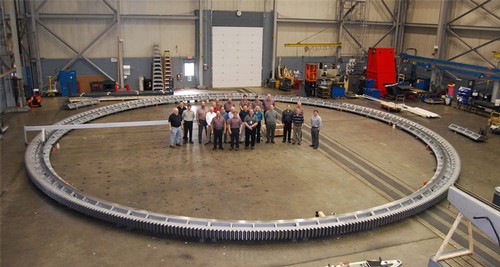
MAG proved it knows how to use machine tools, as well as build them, by developing a process that used a horizontal boring mill (HBM) and specially designed tools to cut 588 teeth in a 19-meter (62.5 ft) diameter gear assembly weighing 60 tons (54,836 kg).
The two-piece gear assembly, made of ASTM A290 steel, consists of a 24-section track, which serves as the base, and a 12-section upper gear rack. The MAG team designed dedicated fixtures for each operation and special tooling for cutting and finishing the gear teeth on an HBM. "We cut the gear teeth on an unconventional machine," said Mark Huhn, project manager at MAG Fond du Lac. "In most cases the tooth involute would be generated by the machine itself, but we used a tool with the involute built into the cutter, which was accomplished by grinding the tooth form into the cutter first." The gear teeth were manufactured to American Gear Manufacturers Association (AGMA) Gear Quality No. 6, and the gear was assembled to a pitch diameter concentricity of .8 mm (.031 in).
The track, comprised of A148M Grade 620-415 castings, required a special cutter to produce a 2.127 degree surface angle. "The angle was circular interpolated onto the track surface and we designed a special cutter to cut the angle on one of our gantry-type machining centers," said Huhn.
Gear Specs
For "gear aficionados," here are some specifications:
>20˚ full-depth, involute teeth cut in accordance with AGMA 201.02
>Pitch Diameter = 19,016.2 mm (748.6693 in)
>Circular Pitch = 101.6 mm (4.0 in)
>Teeth per segment = 49
>Fillet Radius: 9.702 mm (0.382 in)
>Addendum: 32.3 mm (1.273 in)
>Min. Dedendum: 40.4 mm (1.591 in)
>Backlash: 2.286 mm (0.090 in) on pinion, 2.286 mm (0.090 in) on rack, 4.572 (0.180 in) total
>AGMA Gear Quality Number: 6
>AGMA Gear Accuracy Standard: AGMA 2000-A88
>Face Width = 230 mm
>ASTM A290 GR.3 CL.E
>SUP. REQ. S1, S2, S3 and S6
>Alloy Steel Forging
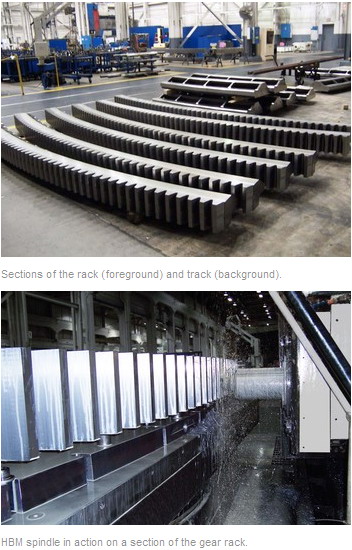
Tags:
Original Hyperlink: http://www.mag-ias.com/index.php?id=1140&L=2..
For more information from this magazine/website? Please click here http://www.mag-ias.com
About Us:MAG is a leading machine tool and systems company serving the durable-goods industry worldwide with complete manufacturing solutions. MAG offers a comprehensive line of equipment and technologies including process development, automated assembly, turning, milling, automotive powertrain production, composites processing, maintenance, automation and software, and core components. Key industrial markets served by these technologies include aerospace, automotive and truck, heavy equipment, oil and gas, rail, solar energy, wind turbine production and general machining.
With manufacturing and support operations strategically located worldwide, MAG ranks as a leader in the capital equipment market. A growing number of leading international companies are relying on the impressive innovation power of MAG to assure their technological leadership and prepare for future challenges.
Note: The copyright and the ownship of the brand, product names, product numbers, and content mentioned belongs to their repective companies.